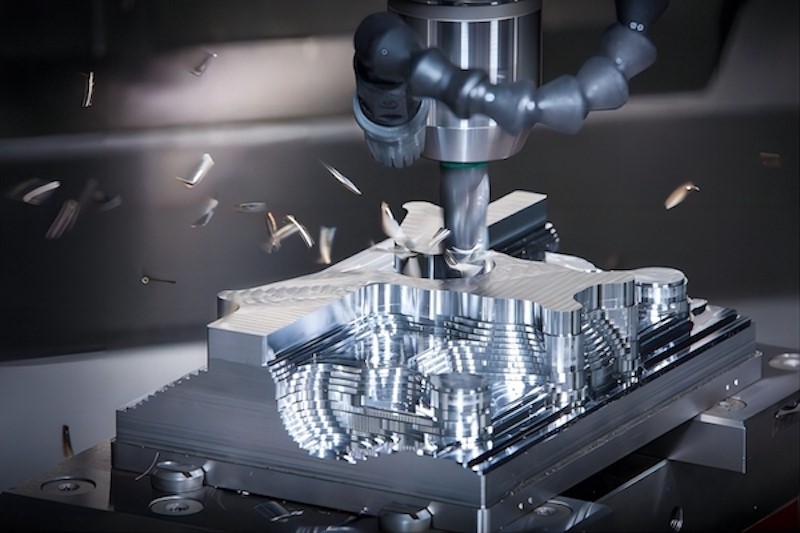
The Basic Foundation block of modern industry, metal fabrication is at the forefront of transforming raw materials like copper, aluminum, and steel, into the components and assemblies that drive everything from aeronautical advances to medical equipment. However, moving from concept prototype to final product is detailed and intricate, comprising cutting-edge technology, technical expertise, and collaboration spanning numerous phases. Because of the particular challenges and advantages of working with CNC aluminum, the process of manufacturing becomes even more accurate when a material like CNC aluminum is used.
In This article, you will get a guide about the important steps in the metal manufacturing process, demonstrating how people and organizations transform ideas into functional products while maintaining, precision, high standards, and affordability.
Initial Concept and Design Phase
Every metalworking job begins with a concept- an idea design, or assembly, that fulfills a certain function. Whether it’s an intricate structural element of a medical device or a lightweight structure of an automotive application the aim at this point is to identify the needs and limitations of the project. During this stage, engineers and designers collaborate to develop a concept prototype that meets the necessary criteria for cost, efficiency, and usability.
To generate complex 3D models of something, CAD software like Solidworks, Fusion 360, Pro-E, and Autocad are usually used. Before manufacturing starts design engineers can utilize these models to identify possible design defects, they can simulate various forces and loads on the component and assess its manufacturability. When designing with CNC aluminum engineers must take into account its distinctive properties, such as lightweight, resistance to corrosion, and the problem posed by its machinability.
Manufacturers can ensure that the design is effective for fabrication and minimize the risk of expensive redesign work or delay by incorporating primary design and feedback from the manufacturing team.
Material Selection: Choosing the Right Metal
Material selection is an essential aspect of any metal production process. The selection of any material directly impacts the product’s functionality and overall performance, corrosion resistance, weight, and durability depending on the purpose for which it is used. aluminum has a good strength-to-weight ratio, great machinability, and recyclable qualities making it an appealing option in industries like automotive, aerospace, and electronics.
Alternate metals like titanium, stainless steel, Mild steel with high carbon, and copper might be used for applications requiring greater strength or more resistant temperature conditions. Each material has strengths and trade-offs that influence the production cost, manufacturing time, and operational outcomes. For example, aluminum is lighter than steel, and it’s easy to machine in less time than steel, but it requires to be handled cautiously to prevent any damage during the whole fabrication process.
Once the material has been chosen, it’s crucial to take into account how it will behave to different loads and stresses and how it will come into account with other parts of the assembly. Engineers additionally have to make sure the material conforms with client requirements and industry standards, particularly in industries like aerospace and medical industry.
Prototyping: From Virtual Models to Physical Prototypes
Prototyping comes following once the design is complete and the material is selected, before proceeding to full-scale manufacturing, fabricators and engineers may use prototypes to confirm the design and its feasibility as well as effectiveness in real settings. A concept design is frequently manufactured using CNC machining, which transforms the CAD model into a real tangible product.
When working with CNC aluminum, it’s highly useful to utilize CNC machining technology because it offers high precision and minute tolerances. aluminum could be machined and formed into intricate shapes using CNC machines, ensuring that the prototype accurately replicates the original design. This stage is essential for identifying possible problems before proceeding on to more longer and more expensive production phase such as assembly issues or material flaws.
With prototyping, manufacturers are also able to get input from stakeholders, designers, engineers, and customers. Any necessary changes can be performed to ensure the final products meet both functional and visual standards.
CNC Machining: Precision and Flexibility in Fabrication
CNC Machining is the backbone of modern metal fabrication. CNCs are automated numerically controlled machines used in machining, like milling, lathe, and drills. Fabricators can cut and shape any metal with high precision and repeatability, it offers versatility as well as quality in the fabrication process. Irrespective of the quantity of parts produced, whether a prototype of thousands of parts.
There are numerous factors to keep in mind when dealing with CNC aluminum. Despite aluminum being highly machinable, it also tends to clog the cutting tools if it’s not handled properly. Manufacturers use aluminum-specific tools and cutting fluids to achieve a certain finish level. In addition, complex cuts and forms that are difficult or nearly impossible to carry out with human methods can be coded into the CNC machine with ease.
Given that the CNC techniques are flexible, they can be used for large-scale production and low-volume customized projects. For industries like the aerospace and medical sectors, where parts must conform to tight tolerances along with the functionality requirement, this flexibility is very crucial.
Throughout the metal fabrication process, quality control is an ongoing and most important concern, where every job is examined at every stage of the manufacturing to ensure it meets requirements for performance, material specifications, and tolerances. Regular evaluations, including a comprehensive downtime report, help identify inefficiencies and maintain optimal workflow.
Welding and Assembly: Bringing Components Together
After single parts are machined, they often require to be joined using different methods, like welding, fastening, and other joining techniques especially when welding aluminum, experienced welders are required with knowledge of metal characteristics. Because aluminum has a lower boiling point than other metals like steel, improper handling can cause distortion or deformation.
When aesthetics and accuracy are required TIG (Tungsten inert gas) welding is often used for aluminum. This welding technique produces better, cleaner, and higher-quality welds, making it ideal for applications where strength and visual appeal are required. The assembled components are often tested after the welding process to ensure strength and quality standards.
Manufacturers may employ robots in the assembly lines to automate the welding process for more complex geometries.
Surface Finishing: Enhancing Durability and Aesthetics
Once the part is assembled, the surface finishing processes are carried out to enhance its toughness, appearance, and corrosion resistance. The method used for aluminum that’s is anodizing which creates a protective oxide layer to ward off corrosion and improve wear resistance.
Following the demand of the customer and the intended application of the product various other techniques are used for surface finishing, like powder coating, electroplating, and painting. In some cases, polishing and buffing are used for a glossy finish.
The overall performance of the finished product is greatly often determined by its surface finish, particularly in electronics and automotive sectors where esthetics are very important for drawing and retaining customers.
Quality Control and Inspection
Throughout the metal fabrication process, quality control is an ongoing and most important concern, where every job is examined at every stage of the manufacturing to ensure it meets requirements for performance, material specifications, and tolerances.
Various testing techniques like non-distractive testing (NDT), ultrasonic testing, and x-ray tests are used for different applications like aerospace and the medical industry to find hidden defects, etc.
Manufacturer ensures that the final products meet customer demand and industry standards by maintaining rigorous quality control standards. To verify that the product complies with regularity standards external validations are sometimes necessary.
Conclusion
The process of turning a prototype into a finished product is extensive and diverse. Metal fabrication requires careful planning, advanced machinery, and collaboration between teams, particularly when working with materials like CNC aluminum, by following an organized approach covering design, material selection, prototyping, assembly, and quality control, the manufacturer can transform raw materials into precisely manufactured, efficient components, that drive global innovation across various industries.
Also Read: